Recycling has become a cornerstone of efforts to promote sustainability and reduce the environmental impact of waste. In the realm of plastic recycling, Post-Consumer Recycled (PCR) plastics play a pivotal role. PCR refers to materials that have been reclaimed from waste generated by consumers, then cleaned, processed, and remolded for reuse.
There are two primary methods of recycling PCR plastics: mechanical and chemical. Mechanical recycling involves physically breaking down plastic waste into small pellets, which can then be remolded into new products. Chemical recycling, on the other hand, breaks down plastics at the molecular level, allowing the creation of plastics that are as pure as original or ‘virgin’ materials.
Why distinguish between these methods? Each has unique strengths and challenges that make them suitable for different types of waste and applications. Mechanical PCR is efficient and well-established but may not achieve the purity needed for certain products. Chemical PCR can process more contaminated or complex plastics and achieve higher purity but is often more resource-intensive.
Understanding the differences between mechanical and chemical recycling is key when deciding how to best manage plastic waste and reduce our environmental footprint. This knowledge enables manufacturers, policymakers, and consumers to make informed decisions and support recycling methods that align with their sustainability goals.
Advantages and Limitations of Mechanical PCR
Mechanical PCR (Post-Consumer Recycled) plastics are created through a process of grinding up plastic waste into small flakes, washing it, melting it down, and then reshaping it into new products. This method is one of the most common and straightforward ways to recycle plastics.
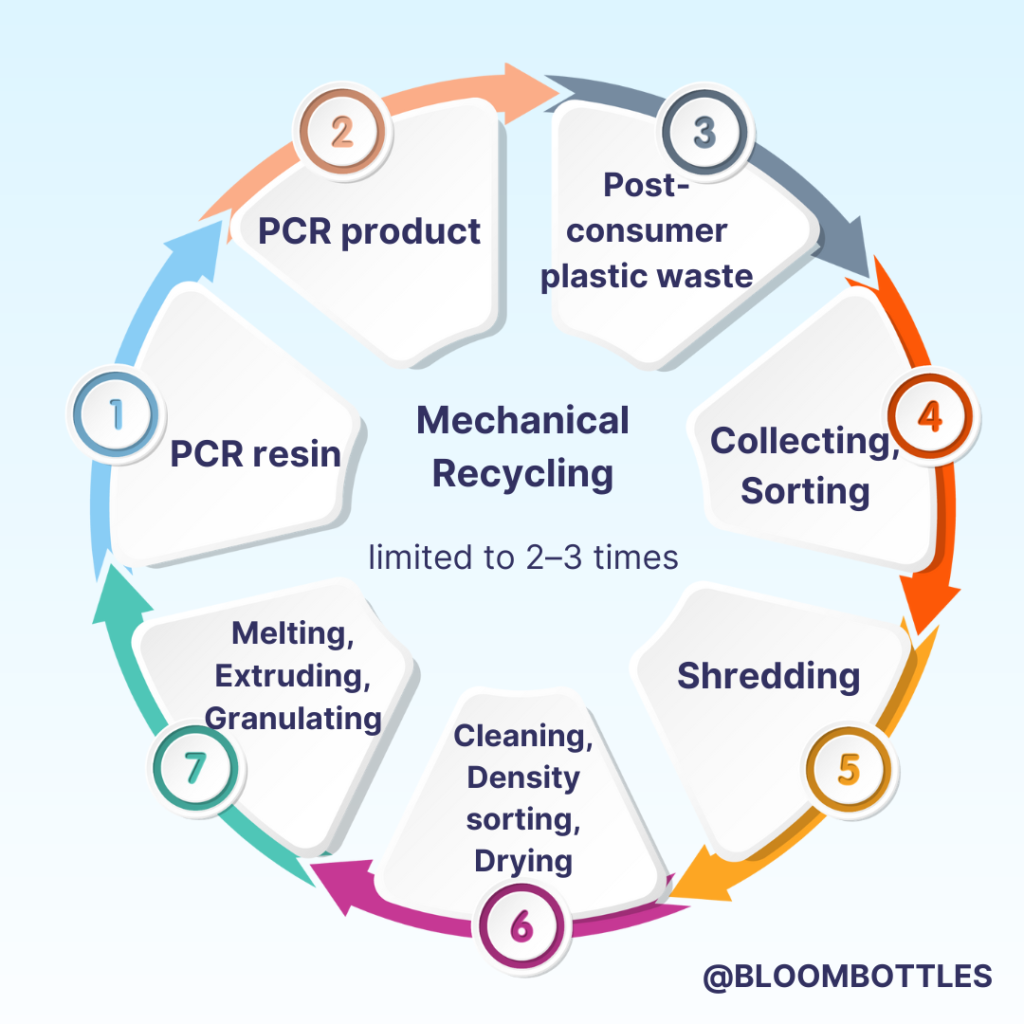
Advantages of Mechanical PCR:
- Energy and Cost Efficiency:
- Mechanical recycling stands out as a process that demands minimal energy, making it an environmentally friendly and cost-effective option for managing plastic waste.
- Material Reuse: By not altering the plastics’ chemical structure, mechanical recycling permits multiple reuse and recycling cycles without substantial quality loss, contributing to a closed-loop system.
- Infrastructure Availability: It benefits from well-established infrastructure due to its long-standing presence in the recycling industry, with facilities more widely available compared to other methods.
- Public Acceptance: Generally, mechanical recycling is well-understood and supported by the public as a beneficial eco-friendly practice.
Limitations of Mechanical PCR:
- Material Degradation (“Downcycling”): The mechanical recycling process can weaken the plastic’s structure, making it less valuable and reducing quality over time. This effect limits the number of times plastic can be recycled before losing its structural integrity.
- Challenges with Mixed Plastics: Mechanical recycling struggles with composites or mixed materials as the different types of plastic polymers can’t be separated easily through these processes.
- Need for Precise Sorting: Producing a high-quality recycled resin requires meticulous sorting to remove impurities and ensure color uniformity, creating additional steps and potential system strain.
- Limited Applications: Despite maintaining structural strength, mechanically recycled plastics often have a less pristine appearance compared to virgin resins, which can restrict their applications.
- Public Perception and Recycling Participation: Although people support recycling, confusion about the process leads to lower participation rates, with a significant portion of recyclables never reaching proper recycling facilities. This issue highlights a need for more consistent recycling programs to reduce confusion and increase efficiency.
Mechanical PCR is best chosen when trying to recycle single-type plastic waste that is relatively clean and free of contaminants. It’s an effective way to reduce the environmental impact of plastics, particularly for non-food packaging and other applications where the highest purity is not critical. However, due to its limitations in recycling quality, it may not be suitable for all types of plastic waste or for use in food-contact or medical applications.
Advantages and Limitations of Chemical PCR
Chemical PCR (Post-Consumer Recycled) involves breaking down plastic waste into its basic molecular components through various chemical processes. These components can then be reassembled into new, high-quality plastic materials. This method offers a different approach from mechanical recycling by essentially resetting the plastic’s life cycle, enabling the production of new plastics without degrading quality.
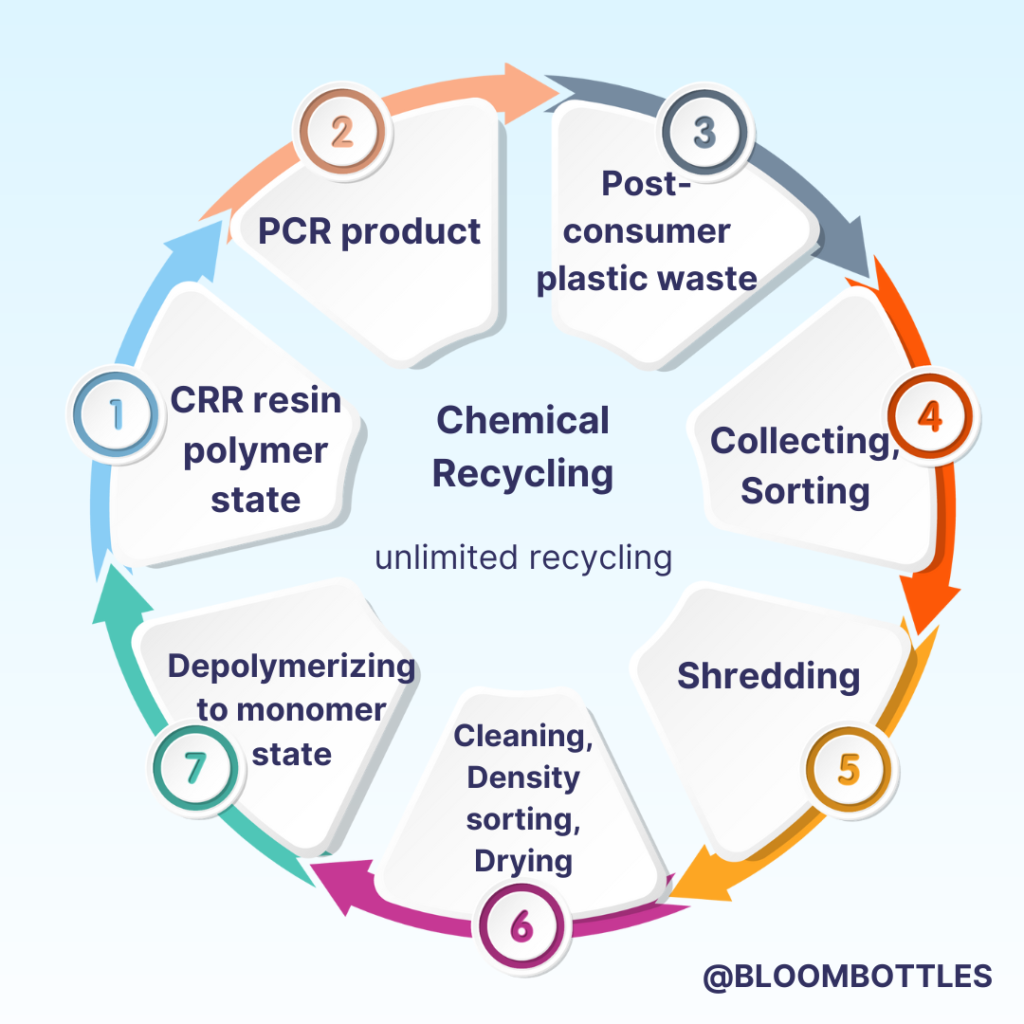
Advantages of Chemical PCR:
- High-Quality Output: Chemical recycling produces plastics of high quality that can compete with virgin materials, providing an end product with similar performance and integrity.
- Versatility in Waste Handling: This process can manage a wide spectrum of plastic waste, including mixed polymers and contaminated materials that mechanical recycling can’t process.
- Repeated Recycling Potential: Unlike mechanical recycling, chemical recycling doesn’t weaken the plastic over time, allowing for repeated recycling without diminishing quality.
- Upcycling Opportunities: Chemical recycling not only recycles waste plastics but also offers possibilities for enhancing the properties of the end product, known as upcycling.
- Less Fossil Fuel Dependence: Transforming waste into new plastics, chemical recycling reduces the consumption of fossil fuels relative to traditional plastic production, presenting a promising route to sustainability.
Limitations of Chemical PCR:
- Higher Energy Use: The overall energy consumption for chemical recycling is notable, and concerns have been raised about the process’s environmental merits.
- Complex Infrastructure Needs: The technology and infrastructure for chemical recycling are complex and still in development, entailing significant investment.
- Increased Costs: Resins from chemical recycling come at a higher price point than those from mechanical recycling, and the current lack of established infrastructure adds to the cost challenges.
- Environmental Considerations: The process may generate higher CO2 levels compared to mechanical recycling, and the use of solvents and acids can lead to toxic waste concerns.
- Emerging Public Perception: Awareness and understanding of chemical recycling are still forming, with misconceptions affecting its public image. Additional research is necessary to thoroughly understand and mitigate the environmental impact of chemical recycling.
In essence, chemical PCR presents a promising avenue for recycling plastics that are difficult to process mechanically, offering the potential to produce high-quality recycled materials. However, overcoming its limitations, particularly in terms of cost, energy consumption, and environmental management, is crucial to fully realizing its benefits for a sustainable future.
Mechanical PCR (Post-Consumer Recycled) plastics and Chemical PCR plastics have several differences in their applications due to the inherent properties and qualities of the recycled materials they produce.
Applications of Mechanical PCR Plastics:
- Packaging: They are commonly used in less-demanding packaging applications such as containers for detergents, beauty, cosmetics, personal care products, and non-food items.
- General Use Products: Ideal for manufacturing various general use items like bins, trays, and non-critical components in consumer products.
- Lower-Cost Goods: Frequently chosen for goods where cost-effectiveness is prioritized over high material purity.
- Non-Food Contact: Suited for applications that do not involve direct contact with food or stringent purity requirements.
Applications of Chemical PCR Plastics:
- High-Quality Packaging: Suitable for food-contact packaging due to its ability to create plastics with a purity level close to virgin materials.
- Medical Applications: Chemical PCR plastics can be used in medical devices or pharmaceutical packaging where high standards of cleanliness and material integrity are critical.
- Specialized Products: Ideal for specialized, high-performance products requiring specific material characteristics unaffected by the previous life of the plastics.
- Upcycling: Allows the creation of new products with enhanced qualities or performance characteristics, expanding the potential for innovative uses beyond simple material replacement.
In summary, mechanical PCR plastic is more suited to applications where material purity and performance are less critical, making it a cost-effective choice for a wide range of uses. In contrast, chemical PCR plastic is favored in higher-value markets and applications where the virgin-like quality of the recycled material is a clear advantage, such as packaging with stringent safety standards, high-end consumer products, and medical-grade applications.
Differences Between Mechanical PCR and Chemical PCR Recycling:
Infrastructure:
Mechanical recycling boasts a well-established network of facilities globally, while chemical recycling, being newer, does not have as extensive an infrastructure, leading to higher setup costs.
Environmental Impact:
Mechanical recycling is generally more energy-efficient but depends more on fossil fuels. Chemical recycling may produce purer plastic but could also result in more hazardous waste due to the chemicals involved in the process.
Purity Level:
The Mechanical recycling is less pure than chemical PCR, meaning it may contain some level of impurities or leftover residues from the original use, it can appear less clear or more discolored compared to virgin plastic. Chemical PCR can remove almost all contaminants, resulting in a very high purity product. The color is similar the same as virgin plastic.
Quality of Recycled Plastic:
Chemical recycling produces high-quality plastic that maintains integrity through multiple life cycles and can be used for more demanding applications. Mechanical recycling, while simpler and more cost-effective, may degrade the plastic’s strength over time, yielding a product of lower quality with each recycling round.
Market Use:
Mechanical PCR is more prevalent in the market currently due to its simplicity, cost savings, and lower energy consumption, making it suitable for a broad range of products that do not require very high-grade materials.
Future Outlook:
The choice between mechanical and chemical PCR depends on the end product’s requirements for purity, clarity, and quality. Mechanical PCR is typically the more energy-efficient and cost-effective method but may produce less pure material. On the other hand, chemical PCR produces a very clean and pure product, suitable for more demanding applications, It is especially noted for its ability to process plastics that are not viable for mechanical recycling and delivering high-quality recycled materials. Though chemical recycling currently faces challenges with higher costs and technological complexities, it is expected to gain a greater market share as the technology matures. These differences are essential for us to consider when deciding on the type of recycled plastic for their products and packaging.
Summarizing the Discussion and Looking to the Future
After exploring the characteristics, advantages, and limitations of mechanical and chemical PCR (Post-Consumer Recycled) plastics, as well as their distinct applications, we can draw several conclusions and consider the future direction of the recycling industry.
Mechanical PCR: This process is cost-effective and energy-efficient, suited for a variety of applications where absolute purity is not necessary. Advances in technology could further improve the quality and reduce the costs, making it a more competitive option.
Chemical PCR: While more costly and energy-intensive, chemical recycling produces high-purity plastics that can be used in sensitive applications, including food-grade packaging. Innovation in this area could lead to more efficient and environmentally-friendly processes.
Future Trends and Industry Recommendations:
Technological Innovation: Continued research and development in both mechanical and chemical recycling processes will be vital. New technologies could lower costs, improve efficiency, and expand the types of plastic waste that we can recycle.
Regulatory Support: Governments could provide incentives for recycling industries, such as subsidies for using recycled materials or penalties for generating plastic waste, to encourage the growth of PCR markets.
Environmental Impact: Both recycling methods need to continue focusing on reducing their environmental impact by using renewable energy sources and minimizing water usage and chemical waste.
Consumer Education: Increased awareness about the benefits of PCR materials can lead to greater consumer demand for products packaged in recycled plastics, thereby supporting the market for PCR.
Global Collaboration: A collective effort across countries, industries, and governments to establish standards and share best practices can ensure the longevity and sustainability of the recycling industry.
While both mechanical and chemical PCR currently have their place in the recycling industry, innovation and regulation will likely shape their future growth and sustainability. By choosing the right type of PCR for the right application and continuing to improve recycling methods, we can make significant strides towards a circular economy and a more sustainable future.
Practical Considerations and Solutions for Mechanical PCR Packaging
At BLOOM BOTTLES, we offer customized mechanical PCR packaging solutions for beauty and personal care brands. Here’s how we address common concerns:
- Cost Considerations: PCR materials cost about 1.4 times more than pure materials. Costs vary with PCR percentage, capacity, and weight. Lower PCR content reduces costs.
- Color Variations: Different batches of PCR materials may show slight color differences. PCR PET is bluish, PCR PE yellowish, and higher PCR content results in darker colors.
- Quality and Defects: Minor defects like black spots may occur, but overall quality is about 90 percent of pure materials. These are small issues and do not significantly impact the product’s functionality.
Production Issues and Solutions
- Solution for Cost Concern: While PCR costs more, it supports sustainability. We help you find the right balance between PCR content and cost to meet your budget and environmental goals. We offer options from 10% up to 100% PCR content, tailored to meet different client needs.
- Solution for Color Differences: We recognize the importance of consistent colors for brand recognition. Our team of experts will work closely with you, providing detailed information about any color variations. We’ll manage these differences to ensure your brand’s packaging remains consistent across different batches, within an acceptable margin of error.
- Solution for Quality Concerns: Despite minor defects, our PCR products meet high-quality standards, comparable to 90 percent of pure materials. We ensure rigorous quality control to minimize defects.
- Trend Adaptability: We keep up with market trends, PET PCR is the most popular in North America, followed by PE and PP. Both transparent and solid colors are available to meet various customer preferences.
- Compliance and Certification: Our PCR materials are certified to the Global Recycled Standard (GRS), providing reliable and eco-friendly solutions.
- Personalized Service: We provide one-on-one professional consultation to help you understand how our PCR packaging aligns with your brand values and market positioning.
- Innovation and Sustainability: We continuously explore innovative methods to enhance the performance and range of applications for PCR materials while minimizing environmental impact.
Choose BLOOM BOTTLES for more than just high-quality PCR plastic packaging; choose a long-term partner that aligns with your brand’s commitment to sustainability and success.
Get in Touch
Interested in our PCR packaging solutions? Contact us today to learn how we can create sustainable packaging tailored to your brand’s needs.